What is Predictive Maintenance?
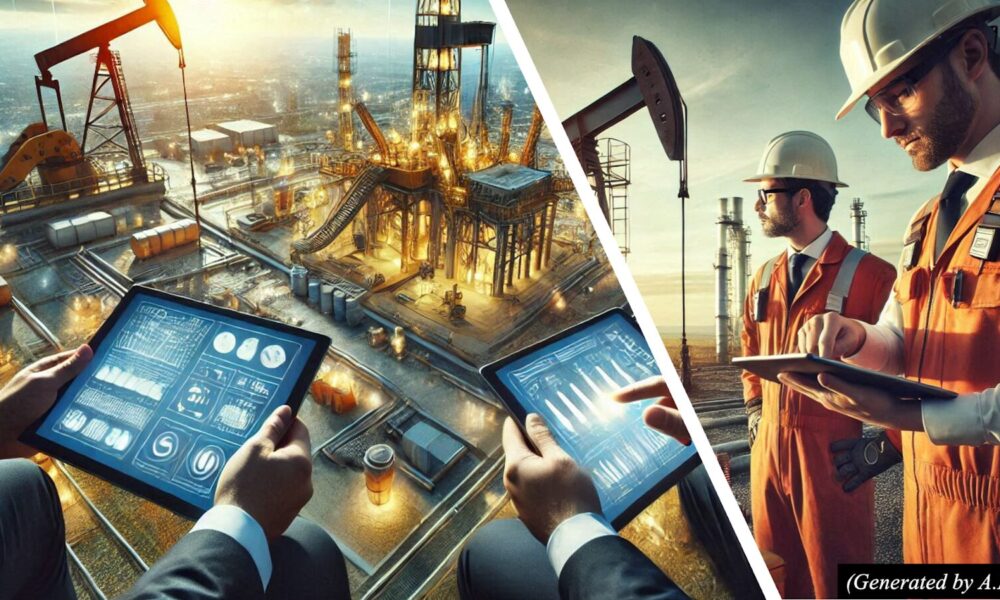
Predictive maintenance is a concept in which, based on certain inputs, the condition of the machine is assessed, and potential failures are predicted. Based on those failure predictions the maintenance activities are performed on the machine. The benefit of this approach over the traditional breakdown, corrective and preventive maintenance is huge. The productivity of the machine can be maximized and unexpected failures can be avoided, which may have huge costs, not only because of the maintenance but also because of the lost productivity.
With the advent of technology, availability of connected sensors, IoT (Internet of Things), ML (machine learning) and AI (artificial intelligence), predictive maintenance is fast becoming a practical solution. The sensors when installed on the machines can send real time data on the condition of the machine, for ex. temperature of a turbine shaft or vibration of a bearing. Trends can be analyzed on these real time readings and based on those trends an abnormal condition can be predicted before it actually happens.
As an example, the rate of vibration of a bearing can be monitored over a period of time and the increase in the vibration can be studied. Based on this increase, rules are defined to predict when the vibration will reach the breaking point (which again can be learned by observing the vibration data from similar bearings). Relying on this predicted failure date the next maintenance can be planned well in advance by ordering the right parts, scheduling the maintenance crew and finalizing a date to have minimal impact on production capabilities due to the down time of the machine.
However, as with everything else, predictive maintenance also comes with some challenges. The data collected by all the connected sensors is huge. Also, a lot of historical data is required to train accurate models which can predict the failures with accuracy.
We’ll now evaluate the pros and cons of predictive maintenance. Like any technology, predictive maintenance also has some benefits and some shortcomings. I’ll try to assess what advantages and disadvantages it brings.
Pros / Advantages of Predictive Maintenance:
- Increased Uptime of Machines: With predictive maintenance and accurate models the failures of the machine can be anticipated in advance, and with minor corrective maintenance, breakdowns can be avoided. This increases the uptime of the machines and thus improves productivity.
- Increased Safety: Sometimes breakdowns may result in hazardous conditions for maintenance workers. A belt on a compressor may snap which may seriously hurt a maintenance worker in the vicinity. A pressure vessel might explode due to high pressure created by a malfunctioning part, which may impact all technicians/ employees in that section of the plant. With predictive maintenance such failures can be avoided by knowing when to replace the compressor belt, or when to replace the malfunctioning pressure relief valve.
- Reduced Maintenance Cost: If the maintenance planner knows the upcoming maintenance activities well in advance, she/ he can plan it very efficiently by scheduling the technicians or service providers and buying the spare parts well in advance. This advanced planning reduces the emergency personnel costs and urgent parts deliveries and saves a lot of maintenance costs.
- Reduced Failures: MTTF (mean time to failure) and MTBR (mean time between repairs) can be drastically increased with predictive maintenance by avoiding any unforeseen failures or breakdowns.
- Reduced Inventory Cost: With predictive maintenance planners can move away from preventive maintenance, which is more efficient than corrective or breakdown, but still consumes a lot of spare parts by following a set interval for maintenance. With predictive maintenance the replacement of spare parts can be optimized by having real-time feedback of the condition of the part.
Cons / disadvantages of Predictive Maintenance:
- Expensive Initial Set Up: While predictive maintenance can save a lot of maintenance costs over the long run, the initial setup can be very expensive. Currently only the very big organizations can afford it. It needs equipment upgrades, sensors enabled with IoT, network connectivity and huge data storage capabilities. Apart from this, resources with the correct skill set are also rare to find since the technology is new. If you combine all these initial costs, it will mean a substantial initial investment.
- Security: At the backbone of any predictive maintenance solution is connectivity and data, there is always a risk of security. A risk of malware or someone hacking the system to gain access to the data is ever present.
- Increased Efforts: Although the breakdown, corrective and preventive maintenance efforts go down with predictive maintenance, there is still a lot of effort required to interpret the huge amount of data and interpret it into actionable maintenance. Training the models with ML and AI also requires a lot of effort and specialized skill.
- Reduced Manpower Needs: With algorithms doing a lot of monitoring of machines, the need for planners and technicians taking rounds of the plant to take readings etc. goes down. Job loss of existing employees, which can be replaced by more efficient predictive maintenance programs and online sensors collecting data all the time.
- Dependency on Data Accuracy: To define effective and accurate predictive models which can forecast upcoming breakdowns or malfunctions accurately is of utmost importance. Historical data plays a critical role in defining models. If the data used to build predictive models is not reliable and accurate then the models will not be reliable. Lack of data is a serious challenge for implementing an effective predictive maintenance.
Conclusion:
Based on the points above I think predictive maintenance could be very helpful for the efficient upkeep of machines and reduction of overall maintenance costs. In my opinion the best approach for most industries towards predictive maintenance should be to start small, assess the results and then scale. With more advances in the technology and availability of skilled resources predictive maintenance could be the future of maintenance.
About the Author – Amit Saxena
Amit Saxena has done M.S. in Data Science, B.E. in Marine Engineering and works as an Architect in an MNC.
He has more than 22 years of experience in Enterprise Asset Management across various industries and is working towards the usage of AI and ML in improving the Maintenance Processes.